Exploring Rocket Construction: Beyond Metals
Non-metals play an equally important role in the construction of rockets.
#We are making something exciting for space and astronomy fans, check here.
You might find it hard to believe but in the early days of rocketry, wood was used in some early rocket designs. For example, Robert Goddard, one of the pioneers of modern rocketry, used wood in the construction of some of his early rockets in the 1920s and 1930s. However, as rocket technology advanced and the demands placed on rocket materials increased, wood was largely replaced by stronger and more durable materials such as metals and composites.
Earlier☝️ we had discussed about different types of metal alloys used in the construction of rockets, in this article we will visit the non-metallic materials.
Carbon Fiber
Carbon fiber is often used in the construction of rocket payload fairings. This is because payload fairings are typically large and lightweight structures that need to be strong enough to protect the payload during launch and ascent, but also need to be light enough to minimize the weight of the rocket.
Composites made out of carbon fiber have a high strength-to-weight ratio, which makes them an ideal material for use in payload fairings. They provide the necessary strength and stiffness to protect the payload, while also being lightweight and reducing the overall weight of the rocket.
Additionally, carbon fiber composites can be molded into complex shapes, which makes them well-suited for use in payload fairings, which often have complex shapes to accommodate the payload.

While carbon fiber is primarily used in payload fairings, it is also used in other rocket components such as interstages and fuel tanks, where its lightweight and high strength-to-weight ratio provide benefits.
Falcon 9, Atlas V, Ariane 6, Antares, Vega are some of the rockets using carbon fiber composites in the construction of their payload fairing. Falcon 9 and Atlas V also use it in the construction of the interstage.
Carbon Fiber Versus Metal alloys
Carbon fiber offers much better strength-to-weight ratio over metal alloys. It is also stiffer than most metallic alloys, which means it is less likely to flex or bend under load. Further, carbon fiber is resistant to corrosion, unlike most metallic alloys. The downsides are the high cost and the requirement of specialized manufacturing processes.
Ceramic composites
Ceramic materials find its use in rockets due to their high melting points, excellent thermal properties, and resistance to wear and corrosion.
One of the most important properties — they typically do not burn in the traditional sense, as they are highly resistant to combustion due to their high melting point and chemical stability. However, they can still be damaged or degraded by exposure to extreme heat, which can cause them to crack, deform, or lose their structural integrity.
In aerospace applications, ceramic materials are often used to create thermal protection systems that protect critical components from the extreme heat generated during reentry into the Earth's atmosphere. These systems are designed to absorb and dissipate the heat through a process known as ablation, in which the outer layers of the material vaporize and carry heat away from the underlying structure. While the outer layers of the ceramic material may "burn" in this sense, the underlying structure remains intact and protected.
The Space Shuttle used ceramic tiles on the underside of its wings, fuselage, and tail to protect against the extreme heat of reentry.
The SLS, currently under development by NASA, will use ceramic matrix composites in its hot gas valves, which operate at extremely high temperatures.
The Ariane 5 rocket uses ceramic materials in its rocket nozzle, which is subject to high temperatures and wear.
The Atlas V and the Delta IV rocket uses ceramic materials in its engine's combustion chamber and nozzle, which are subject to high temperatures and corrosive gases.
Other Materials for Re-entry heat shields
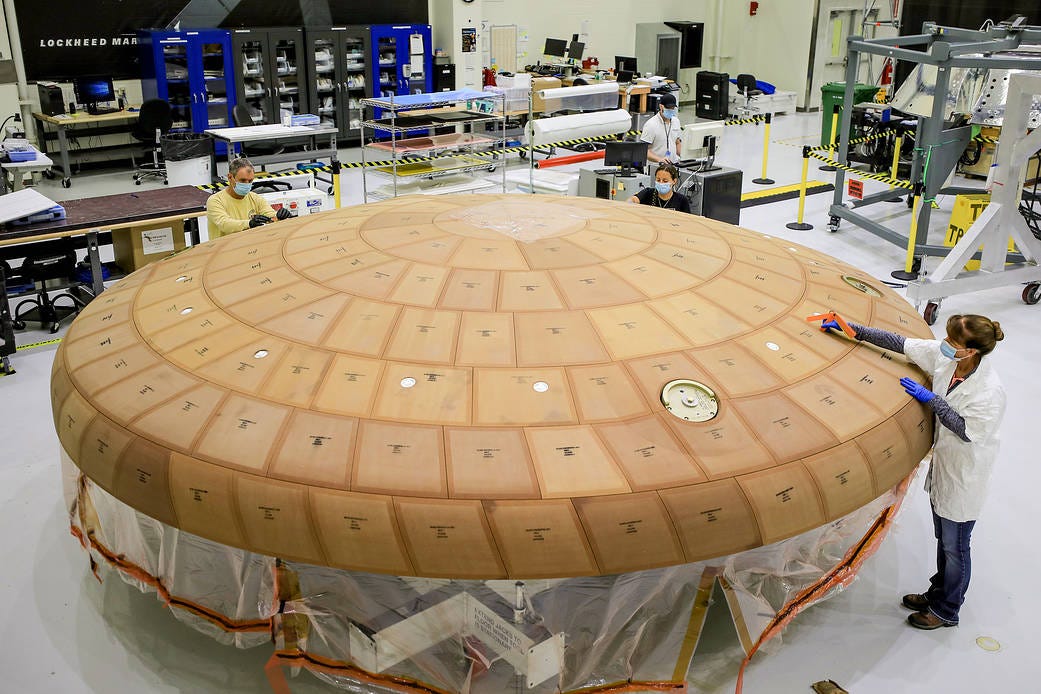
Along with ceramic composites used in Space shuttle, there have been other materials used as heat-resistant materials for their reentry shields as well. For example—
Phenolic Impregnated Carbon Ablator (PICA): PICA was first used on the Stardust spacecraft, which was launched by NASA in 1999 to study comets. It has since been used on a number of other spacecraft and reentry vehicles, including the Mars Science Laboratory, which landed the Curiosity rover on Mars in 2012.
Carbon-Carbon (C/C): C/C is used in a variety of rocket components, including nozzle throats, exit cones, and heat shields. For example, the heat shield on SpaceX's Dragon spacecraft, which is used to transport cargo and crew to the International Space Station, is made of C/C.
Epoxy Resin: The Orion spacecraft uses 180 blocks of ablative material called AVCOAT. It is an epoxy novolac resin with special additives in a fiberglass honeycomb matrix. AVCOAT was used for the heat shield on NASA's Apollo command module
Tungsten: Tungsten is often used in combination with other materials to provide additional protection against the extreme heat of reentry. For example, the reentry shield on China's Shenzhou spacecraft, which is used for crewed missions to space, is made of a tungsten-based alloy in combination with other materials such as carbon fiber.
Kevlar Composites
Kevlar composites are made by combining Kevlar fibers with a polymer resin. The single most important property of Kevlar composites are their resistance to impact. Along with offering heat and flame resistance, they are known for their high strength and durability, and are often used in applications that require resistance to impact and abrasion. Some of the usage in rockets are discussed below—
Delta IV Heavy: The Delta IV Heavy rocket uses Kevlar in the construction of its rocket motor cases. These cases help to contain the high-pressure combustion gases generated by the rocket's engines during flight.
Falcon 9: The Falcon 9 rocket uses Kevlar in engine shields, which protects each engine from debris in the event of its neighbor failing.
PSLV: The PSLV rocket uses Kevlar-polyamide in the construction of the casing of its solid motor for the third stage.
Kevlar is used in the parachute cords and straps to provide strength and durability during descent and landing. It is used in the parachute systems of the Orion spacecraft, designed for NASA's Artemis program.
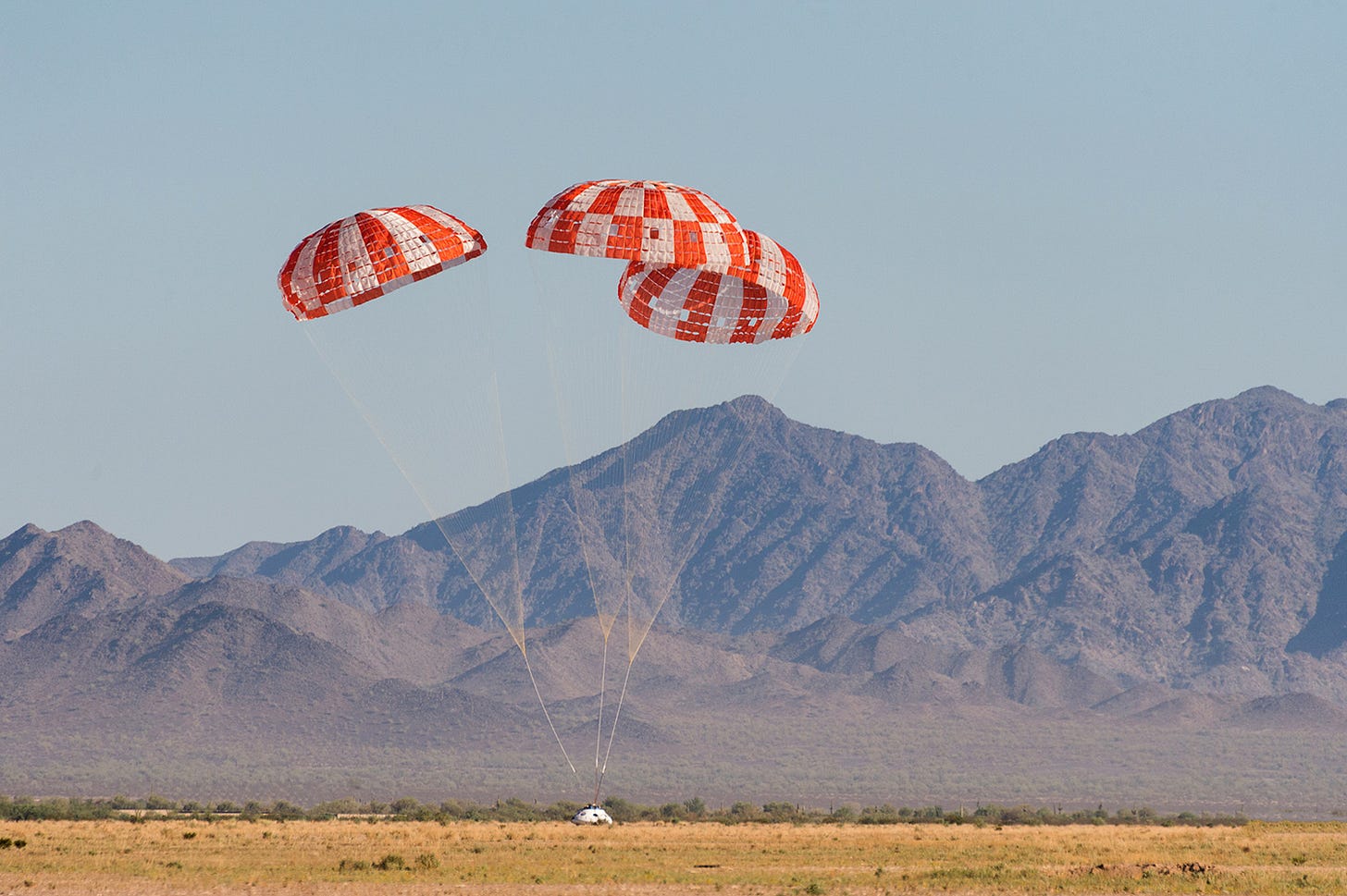
Obsolete materials
At the start of the article we discussed how wood was used earlier in rocket construction. There were many other materials which were extensively used earlier but now have been phased out. Some examples —
Paper: In some of the earliest rockets, paper was used as a fuel material. The paper was coated with a mixture of chemicals and then ignited to produce a burst of flame. However, paper is not a stable or reliable fuel material and has been largely replaced by more advanced solid and liquid rocket fuels.
Bakelite: Bakelite is a type of thermosetting plastic that was used in some early rocket designs for electrical components and other parts. However, Bakelite is not very strong or durable, and has been largely replaced by more advanced plastic materials such as nylon and polycarbonate.
Fiberglass: Fiberglass was used in some early rocket designs for nose cones and other structural components. However, fiberglass is relatively heavy and has poor thermal resistance, making it less suitable for modern rocket designs. Fiberglass has been largely replaced by stronger and lighter materials such as carbon fiber composites.
We hope you found this article informative. In next newsletter we will cover another interesting topic.